Polishing tools and abrasive tools for CNC machine
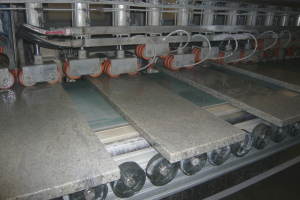
CNC, which stands for Computer Numerical Control, has been applied in the machine tool industry for several decades. The program lets you control aspects such as feeding speed, travel distance, and rotating speed. All of this required a great deal of experience to master. Furthermore, you need to possess a unique type of skill in order to use a CNC machine effectively.
Nowadays, CNC machines are so popular that you will see them being used in most industries. But the problem is that they are still expensive compared to conventional machines and not all types of work are suited for this process. CNC machines are good for large-scale productions or work that involves numerous processes. In the stone industry, the polishing processes are primarily automated by CNC machines, which generate large slabs or slates of granite, marble, and travertine. After you input the required CNC machine tool and grinding settings, the machine will continuously churn out the granite or marble products accordingly.
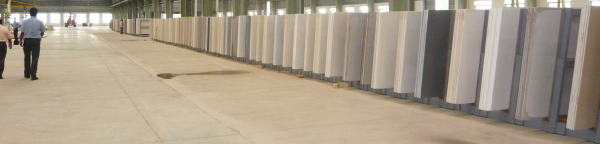
CNC machine tools require more accuracy and stability compared to the radial arm polishing machine. This is because the worker cannot adjust or change the polish settings during the process. If something goes wrong with the tools, the CNC machine will eventually stop or continue producing defective products.
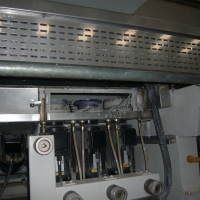
Generally, CNC machine tools can be evaluated by the following points: the surface condition of the stone such as image clarity, color, burn mark, etc. These are the points that are also checked by conventional machine tools but the biggest difference is that during polishing, conventional radial arm polishing can change the polish settings according to the look of the surface, whereas CNC tools are continuously exerted.
A few well-known CNC machine manufacturers for stones are Intermac, Bavelloni, Park Industries, Marmo Meccanica, etc. Our standard CNC tools are mainly designed to be compatible with these CNC machines.